Battery Container
I recently took over as the lead on this project due to time constraints. I’m leading a team through the end of conceptual and preliminary design and into the beginning of preliminary design. Work shown here will be a mix of mine and others with credit where credit is due.
Problem Defintion
The battery container design is largely governed by the rules for the Formula Hybrid competition. The battery container must provide structural support for 64 Li8P25RT battery cells. The container must have room to accommodate any high voltage wiring and fuses needed to connect the cells together and to the high voltage circuitry. The container may also contain the AIRs, AMS, and precharge circuitry as per Formula Hybrid EV2.3.4 but not any elements unnecessary for accumulator operation.
As per formula hybrid EV2.4, the container must be robust, fire resistant, and have insulation if made of a conductive material (EV5.4) including mounting hardware that penetrates the container. The outside of the container must also be connected to the GLV ground. Any ventilation must prevent water entry and minimize fire spread. Any wiring holes must comply with FH EV3.3.1. The accumulator container must be mounted with no less than 4 8mm Grade 8.8 fasteners and be able to withstand 20g vertical acceleration and 40g horizontal acceleration.It is desirable that the container be easily accessible to improve maintenance and recharging. It is also pertinent that the container be as close to the bottom of the chassis as possible to maintain a low center of gravity for the vehicle.
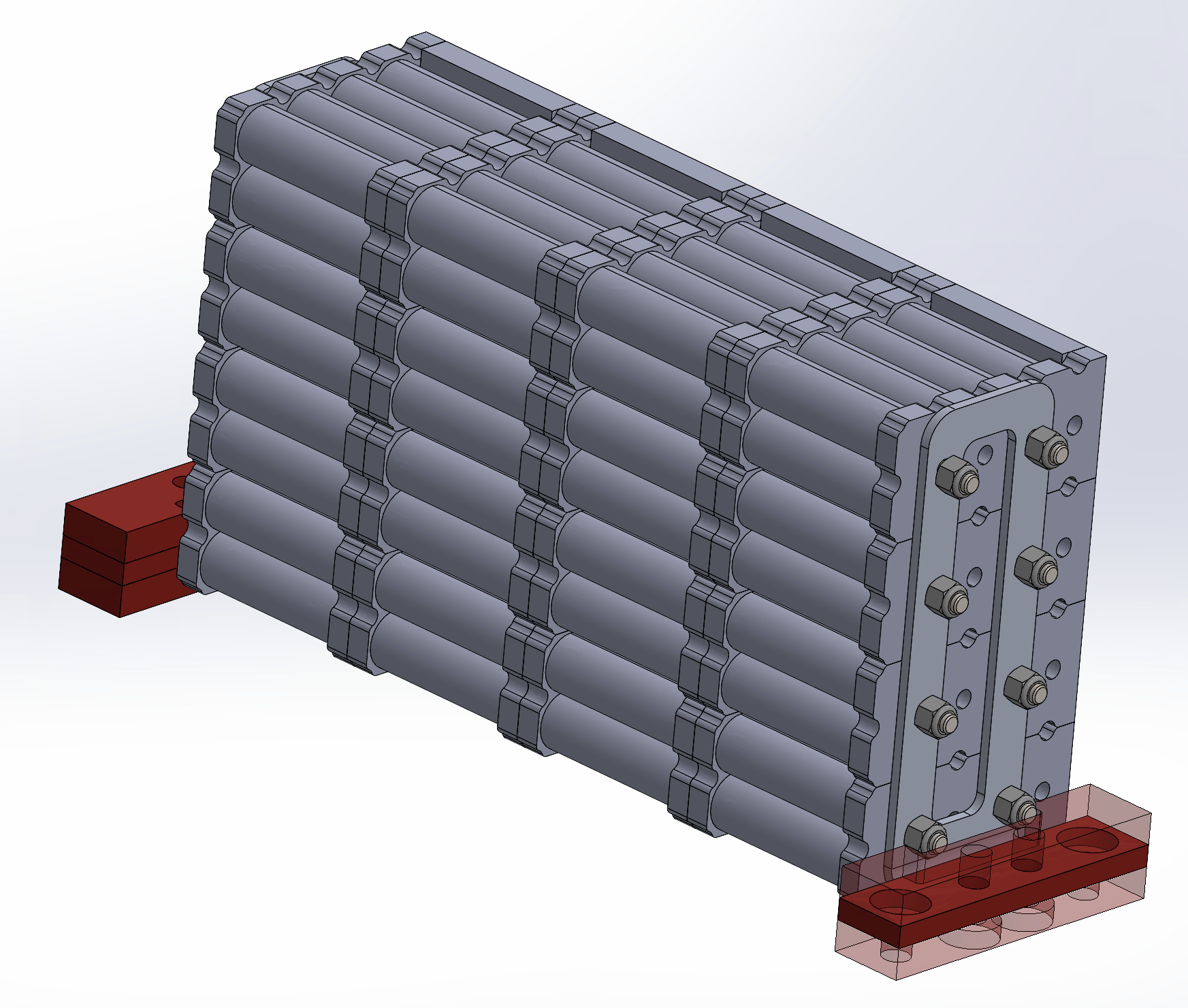
Conceptual Design
Firewall material
Based on the problem statement, I know that the firewall material must be either steel or aluminum. I also know that the manufacturing process for the container will most likely involve bending sheets of the material. It’s also imperative that the firewall material must be resilient to heat, have high tensile strength, and it would be nice for the material to resist corrosion. Using these considerations, I construct a pugh matrix (figure 1) with several aluminum and steel variants offered by McMaster-Carr.
Point Values
McMaster's range of qualitative ratings corresponds to a nice 1, 2, 3 point system, so I used that for all my categories to keep the balancing simple. By using the same 1, 2, 3 range for all categories, I’m able to weigh them in the final tally without first having to balance them with each other. This way, I can assign weight to categories based on how important I deem them to be. For qualitative categories, “Fair” gets a 1 and “Excellent” gets a 3. With the quantitative categories, I plotted the data in bar plots to help divide the data into three ranges and then applied a rating.
Formability
While McMaster does provide their own qualitative measure of formability rated from “Fair” to “Excellent,” I’m not inclined to trust it to its word, and I wanted to dig a little deeper. Thus, I added yield strength, young’s modulus, and elongation at break to get a better sense of the ductility of the materials being considered. Some materials also didn’t have a qualitative measurement of formability, so I was able to use these parameters to fill in my own. I decided to weigh the McMaster rating as 1 while the yield strength, elongation at break, and young’s modulus get a 0.5 weight. I weighted the McMaster rating higher because, despite my reservations, it correlated well with the data I was able to collect on formability, and the lower weight for my data was so that formability isn’t weighted too heavily in the final tally, as I think having a formability qualitative rating and then another three quantitative categories assigns too much point value to formability as a design consideration.
Density
Without knowing exact dimensions of the part, density is the best way to get a sense of which material will be optimal for building an assembly that meets our objective of reducing weight. The two steel alloys perform horribly in this category while all of the aluminum alloys are indistinguishably good.
Strength
Another important consideration for this design is the strength of the material. Metals have only been considered because of their nearly unrivaled toughness, but it’s important to consider how much stress the material can withstand in the ultimate sense; therefore, we consider ultimate tensile strength. Ironically, the two final considerations (AL3003 and AL5083) didn’t do terribly well in this area, but I’m glad nonetheless that it was considered.
Specific Heat Capacity
Since this material is being used to construct a firewall, I decided it may be a good idea to examine the specific heat capacity of all the materials as well. This, next to cost of course, is one of the more heavily weighted categories. Most of the aluminum alloys performed exceptionally compared to steel, and I was glad to see that the two finalists are two of the better performing in this category. A nice indication that I haven’t completely lost my mind—not yet.
Cost
The ugly elephant rears its head as always. As much as I wish the budget was bottomless, cost is a strong consideration for this build as well.
Electrical Insulator
Formula Hybrid rules also mandate that the inside of the battery container must be electrically impermeable. To achieve this end, a couple electrically insulating materials are examined for use. The electrical team was responsible for determining these materials and deciding which would be most effective for use in this design
Preliminary Design
The preliminary design for the battery containers was an impressive undertaking. The leadership group for Terrier Motorsport collaborated on individual components and were able to produce an initial design to prepare for ESF1 and SES requirements.
Specification Report - Shane McLeod
Shane is a member of the wheels team at Terrier Motorsport. He was able to look through the rules and summarize all structural and electrical requirements for the batteries. The report was incredibly helpful in speeding up the preliminary models for the batteries.
Container Mounting to Vehicle
Based on the structural requirements of the container, it is ideal to mount the batteries directly to the frame through the container. This way all loads that the batteries are subject to may be transferred through the frame of the car instead of through the walls and structure of the container. The challenge is that the inside of the container must also be completely electrically insulated from the outside. Will Krska, Matt Casavant, and Avery Hellen were able to envision a preliminary setup where the connection between the batteries and the frame is insulated.